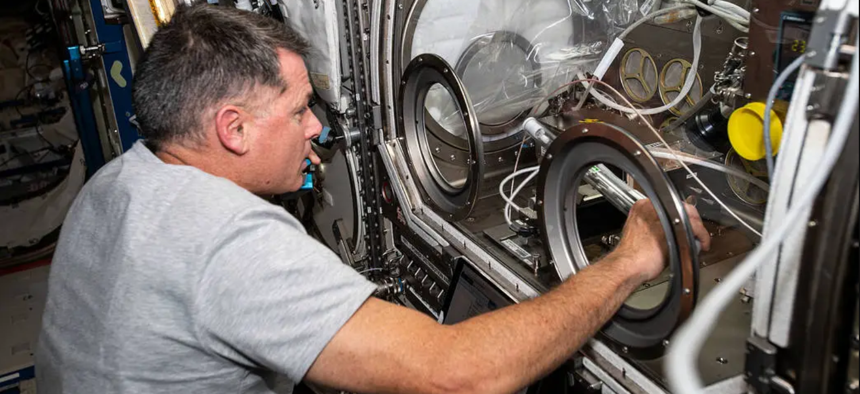
May 21, 2021) — NASA astronaut and Expedition 65 Flight Engineer Shane Kimbrough swaps samples inside the Microgravity Science Glovebox for an experiment called Solidification Using a Baffle in Sealed Ampoules, or SUBSA. The physics investigation explores experimental methods of crystallizing melts in microgravity and is expected to result in reduced fluid motion in the melt, leading to better distribution of subcomponents and the potential for improved technology used in producing semiconductor crystals. NASA
The next push for microchips made in space
The key to higher-quality semiconductor materials could be space.
The United States is expected to face a chip shortage as part of an explosion in artificial intelligence and AI powered devices.
One way to help solve it? Look to space.
In a Government Accountability Office report released Nov. 13, the congressional watchdog suggests that space-based manufacturing of semiconductor crystals has advantages over Earth-based manufacturing. Specifically, the crystals created could have fewer “gravity-induced defects” that can degrade device performance. The idea is part of a report titled, “On the Horizon: Three Science and Technology Trends that Could Affect Society” on scientific developments expected to thrive in the next decade.
Gene-editing to treat diseases and biodegradable bioplastics were the two other technologies the GAO report mentioned.
“Space has a microgravity environment with a natural vacuum and solar energy, all of which could improve certain manufacturing processes such as crystallization,” the report read. “The microgravity environment of space presents opportunities to develop next-generation semiconductor materials, potentially reducing U.S. dependence on specific aspects of foreign supply chains.”
The report points to several advantages. First, liquids and gasses perform differently in microgravity which can lead to greater precision and uniformity of the crystals grown. In addition, because a vacuum exists in space, manufacturers can save the time, energy and dollars necessary to create that condition. Solar energy also is available to power the creation.
Next-generation semiconductors are thought to be necessary for a series of emerging technologies including artificial intelligence, electric vehicles, 6G communications, radar systems, renewable energy systems, and quantum computing.
Scientists and engineers have been considering such a manufacturing idea for decades as experts have warned that the United States may need to rely on foreign nations for some microchip materials. The GAO report’s authors focused on technologies they believed “are demonstrating progression.”
In 2002, crew aboard the International Space Station set up the Solidification Using a Baffle in Sealed Ampoules hardware, or SUBSA. That equipment essentially acts as a high-temperature furnace that helps study how microgravity affects the semiconductor and scintillator crystals.
Then in a 2009 report from the National Research Council of the National Academies titled “Frontiers in Crystalline Matter: From Discovery to Technology,” the authors wrote that if current trends continued, “U.S. scientists, engineers, and industrial facilities either will become dependent on materials developed and grown outside the United States or will not have access to needed materials at all.”
Asia is now thought to control about 70% of the high-purity crystalline silicon market, the GAO said.
And in March 2023, Stanford University hosted a workshop on “Semiconductor Manufacturing in the Space Domain.” A group of experts said in a whitepaper they hoped to make space manufacturing a reality by 2050.
“Transitioning this industry into space is the only path forward if the United States is to keep pace with the technological arms race unfolding across the globe,” the paper read.
But the process is not without disadvantages. Launching materials to space is expensive. In addition, such factories in low Earth orbit could become a target to competing nations. Perhaps most notably, the GAO points to estimates that an Earth-based silicon crystal production facility could cost about $5 billion. A space-based one could cost more.
“Large capital investments would be required to establish space-based, automated semiconductor manufacturing infrastructure,” the report reads.
The report also notes it is unclear how international law treats products made in space.